I looked at my queue of posts to write today and realized that I’ve been slacking since March. That is about the long and short of the year so far. With the pandemic shutting things down in March, followed by what has to be one of the hottest summers I can recall, I haven’t had a chance to do much woodworking this year.
But Mousie, thou art no thy-lane,
To a Mouse – Robert Burns
In proving foresight may be vain:
The best laid schemes o’ Mice an’ Men
Gang aft agley,
An’ lea’e us nought but grief an’ pain,
For promis’d joy!
To say that this is a disappointment is an understatement. I had arranged to teach a class on kalimba making this summer. Unfortunately, that was cancelled due to the pandemic. The plan for the year was also to do at least one show. It appears most craft shows have been cancelled or are severely cut down. Add to that some of the other goings on since March and there is just no way I’ll have enough stock to do a show this year. That, of course, is no excuse for not getting what items I do have in stock photographed and up on the website for sale.
While I was able to travel to The Woodwright’s School in June for classes with Roy Underhill and Cara O’Connell, the whole experience was a bit surreal. Roy and Cara did a great job given the circumstances. Ed Lebetkin’s tool store, located above the school, was open to those of us in classes. This place is like a candy store for woodworking tools. I ended up leaving with a new rip panel saw, a 6 inch Starrett combination square, and a small incannel gouge. On the way down to Pittsboro, I stopped in Thurmond, WV, a ghost town in the bottom of the New River Gorge. The thing is, most of the places I drove through felt a bit like Thurmond – eery and abandoned. I stayed at the Celebrity Dairy, bed & breakfast and working goat farm, located between Siler City and Pittsboro. Fleming and Brit were wonderful hosts.
Main Street, Thurmond, WV The Inn at Celebrity Dairy Metal sculpture and other art can be found throughout the grounds. Looking toward the duck pond. Interesting pattern in the building The Woodwright’s School Inside the bench room Ed’s Tool Store
As if the heat this summer weren’t enough to keep me out of the workshop, we also embarked on Operation Kitten Fixin’ in May/June. The feral colony in our back yard produced four kittens this year. The process of trapping them, getting them fixed, and in the case of three of the kittens, socializing them, took a lot of time (and I wasn’t even the person who was doing most of the work!). I’m happy to report that three of the four kittens are now in their forever homes. One of them was captured a bit too late for socialization. The adult cats (minus one who has an appointment coming up) in the colony have also been trapped and fixed. With luck, no more kittens for at least a few years.
Sootball Comet (Orange) and Bernie
I have been able to build a few small projects on the lathe, including some coasters, a ring box, and a small vase. I haven’t taken photos of the coasters as I never applied finish to them. They are doing duty right now, but they really should have received a coat some sort of finish. I have some ideas for doing sets of these, including adding colored resin, but that’ll wait for another day.
The ring box was made during a period of shop cleaning and organizing. I’d started on the box at some point at least a year ago and never completed it. I’m still in the process of figuring out the best way to handle the interior foam/ring holding.
The vase was a bit of an experiment. I had a free day where the temperature in the shop wasn’t atrocious. I also had a scrap offcut of some ash that I had glued up (I can’t recall the original piece). It was a nice enough first go at the form. I painted the base with an oil paint mixed with boiled linseed oil. Danish oil was used for the top finish. The phrase “watching paint dry” clearly refers to oil, not modern latex, paint. Either way, it turned out well and is currently living on our front porch.
After my return from Pittsboro, and having taken a class on Slyod and green woodworking, I was inspired to build a shaving horse. This based on plans I found from Peter Follansbee, though I used only three legs instead of four.
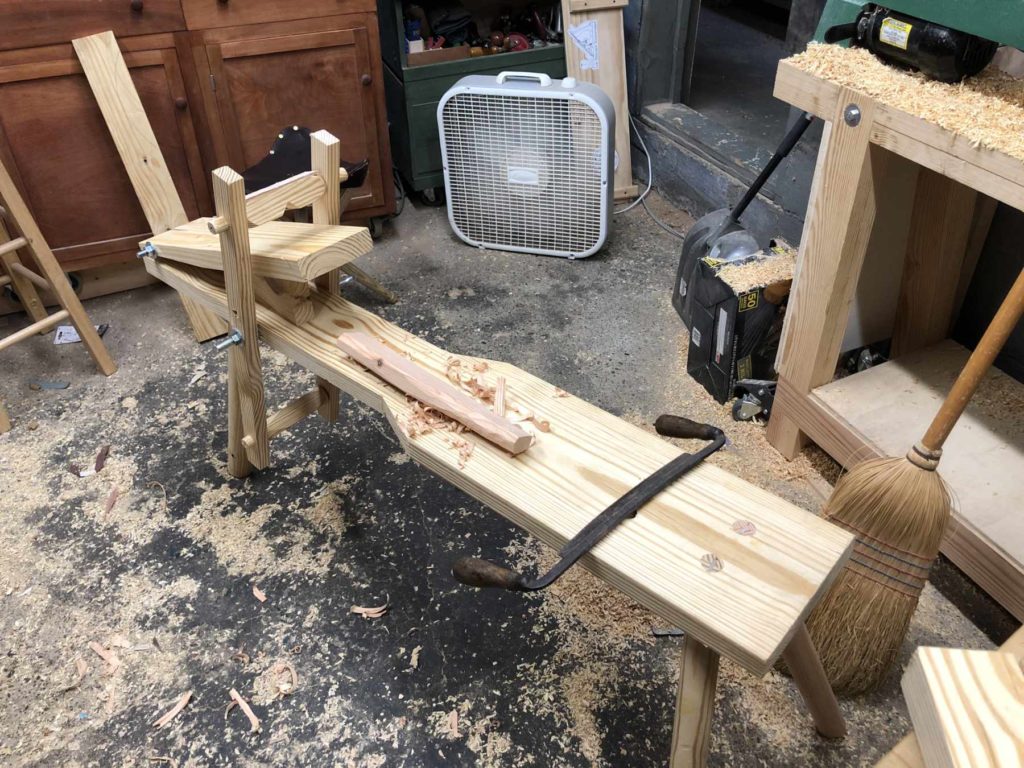
In addition, I designed and build a seiza bench. The bench is about 7 inches off the ground and angled forward slightly. The bench is made from beech with sapele wedges, finished with black wax and danish oil. The seat is an oblong octagon, with an underbevel to reduce its visual weight. The legs are set into shallow mortises that house the full width of the leg. Each leg is further secured with double-wedged double tenons. The shaping of the seat, as well as adjustments to the angle of the legs was a fun exercise. I have some beech left over and may make a small table to match.
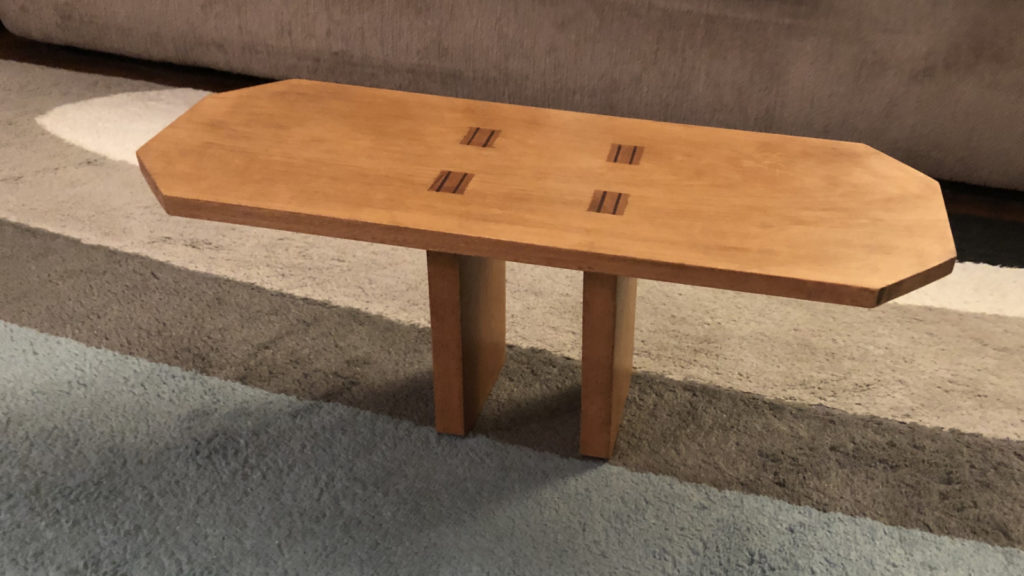
So that’s about the long and short of Wave I of the 2020 pandemic. With luck, the fall and winter will be much more productive and much less devastating for the world.